BMW > M3 & CSL (E46) > H) STYLING, BODYWORK & AERODYNAMICS: INTERIOR & EXTERIOR (* Including carbon fibre items, but please also see seperate Carbon Fibre section above ! ) > - Wheels > BBS
Product Code: bbswhl
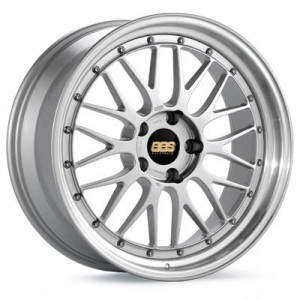
LM MODEL
Click to Enlarge
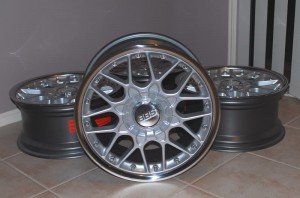
RS II
Click to Enlarge
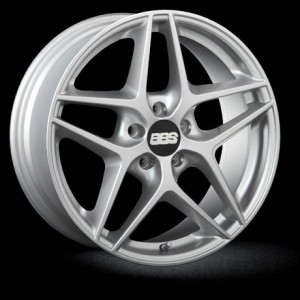
C F
Click to Enlarge
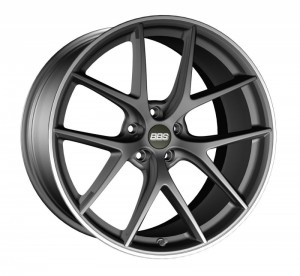
CI R
Click to Enlarge
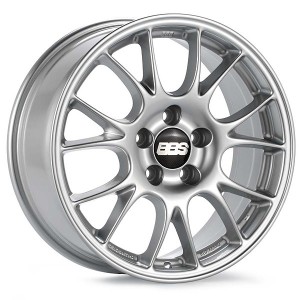
C O
Click to Enlarge
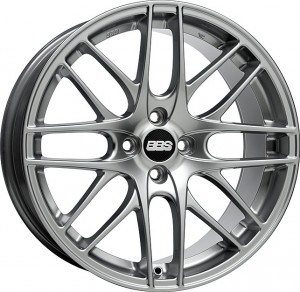
CS 4
Click to Enlarge
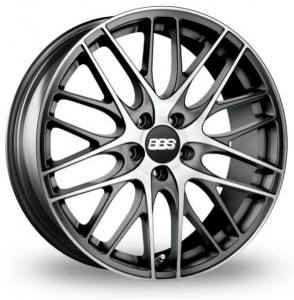
CS 5
Click to Enlarge
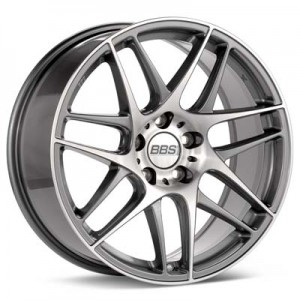
CX R
Click to Enlarge
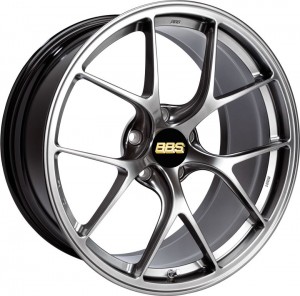
RI D
Click to Enlarge
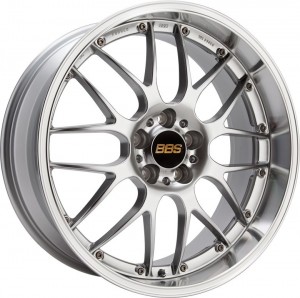
RS GT
Click to Enlarge
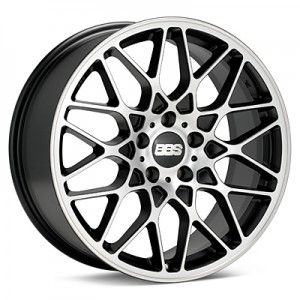
RX R
Click to Enlarge
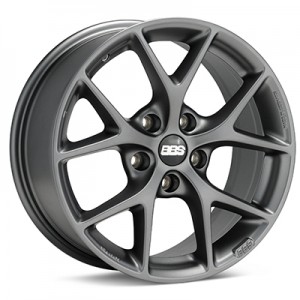
SR
Click to Enlarge

SUPER RS
Click to Enlarge
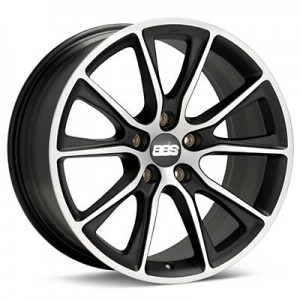
SV
Click to Enlarge
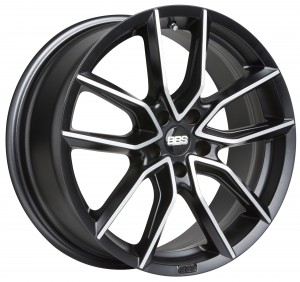
XA
Click to Enlarge
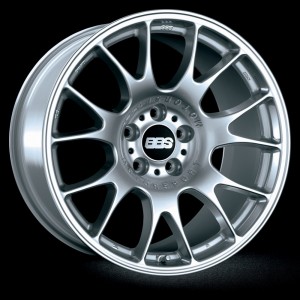
CH
Click to Enlarge

CH R
Click to Enlarge
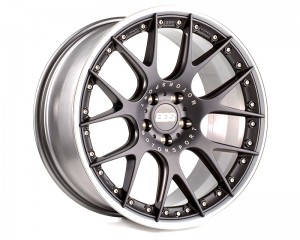
CH RII
Click to Enlarge
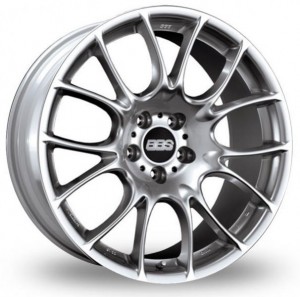
CK
Click to Enlarge
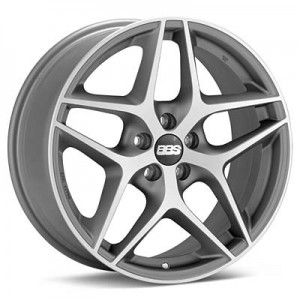
CF
Click to Enlarge
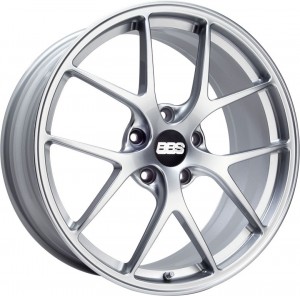
F1
Click to Enlarge
Description
A world renowned ultra high quality wheel manufacturer that hardly needs any introduction !
PLEASE SEE PRICE LIST LINK AT BOTTOM OF THIS PAGE. WE WILL BEAT ANY OTHER QUOTE.
Each individual BBS product is the result of state-of-the-art engineering and the most innovative production methods. But it is also the essence of more than 35 years of experience in international motor sport and close cooperation with distinguished automobile manufacturers and European universities. This is the provenance that makes our products unique. And the enthusiasm for things that are special accompanies each of our development and production processes right up to the finishing. With only one goal in sight: the perfect result.
FORGED LINE
Forging is a non-cutting forming process for material in a heated, solid condition. In order to generate the highest degree of material density and weight reduction at top performance from our high-strength and durable aluminum or magnesium alloys, they are further enhanced in a complex forging process. This entails placing the heated star hub or the entire wheel blank in a press and compressing it in several work steps at 5000 to 8000 tons of closing pressure to further densify the material in a special form known as a matrix. In between the individual work steps, the blank is repeatedly heated to approx. 400 degrees centigrade. As a result an optimal material structure is achieved particularly at the areas of high strain, the wheel can be dimensioned smaller, and is thereby lighter in weight.
PERFORMANCE LINE
Flow forming uses hydraulic rollers to achieve greater density in the material structure for the rims of our light alloy wheels. The rim well of the over 300 to 350 degree centigrade hot wheel blank is kept in a continuous rotational motion under high pressure and at high temperatures, and subsequently rolled out over a cylinder in one work step.
DESIGN LINE
To produce a really perfect and long-lasting wheel, it is essential to have a top-quality casting blank. We use the low-pressure aluminum casting technique to manufacture this base for our light alloy wheels. This involves pressing the aluminum alloy into a multi-part mold with up to 2 bars of pressure. After it has cooled down to approx. 400 degrees centigrade, the mold is opened and the casting blank is transported to the initial material test on a conveyor belt. Low-pressure aluminum casting is an extremely sophisticated technology and requires that our employees have expert knowledge and be highly experienced.
PLEASE SEE PRICE LIST LINK AT BOTTOM OF THIS PAGE. WE WILL BEAT ANY OTHER QUOTE.
Each individual BBS product is the result of state-of-the-art engineering and the most innovative production methods. But it is also the essence of more than 35 years of experience in international motor sport and close cooperation with distinguished automobile manufacturers and European universities. This is the provenance that makes our products unique. And the enthusiasm for things that are special accompanies each of our development and production processes right up to the finishing. With only one goal in sight: the perfect result.
FORGED LINE
Forging is a non-cutting forming process for material in a heated, solid condition. In order to generate the highest degree of material density and weight reduction at top performance from our high-strength and durable aluminum or magnesium alloys, they are further enhanced in a complex forging process. This entails placing the heated star hub or the entire wheel blank in a press and compressing it in several work steps at 5000 to 8000 tons of closing pressure to further densify the material in a special form known as a matrix. In between the individual work steps, the blank is repeatedly heated to approx. 400 degrees centigrade. As a result an optimal material structure is achieved particularly at the areas of high strain, the wheel can be dimensioned smaller, and is thereby lighter in weight.
PERFORMANCE LINE
Flow forming uses hydraulic rollers to achieve greater density in the material structure for the rims of our light alloy wheels. The rim well of the over 300 to 350 degree centigrade hot wheel blank is kept in a continuous rotational motion under high pressure and at high temperatures, and subsequently rolled out over a cylinder in one work step.
DESIGN LINE
To produce a really perfect and long-lasting wheel, it is essential to have a top-quality casting blank. We use the low-pressure aluminum casting technique to manufacture this base for our light alloy wheels. This involves pressing the aluminum alloy into a multi-part mold with up to 2 bars of pressure. After it has cooled down to approx. 400 degrees centigrade, the mold is opened and the casting blank is transported to the initial material test on a conveyor belt. Low-pressure aluminum casting is an extremely sophisticated technology and requires that our employees have expert knowledge and be highly experienced.
Additional Information
BBS WHEELS PRICE LIST 15